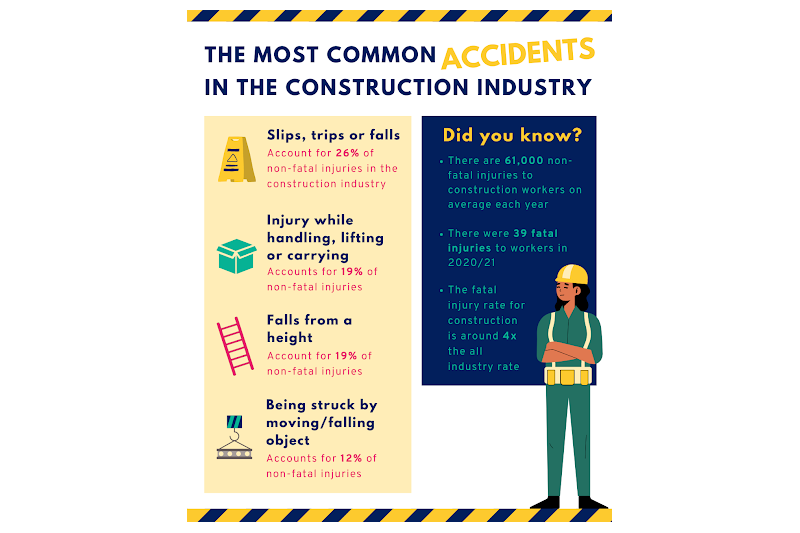
Injuries and ill-health in the UK construction industry are now costing upwards of £16.2 billion, new data has revealed.
Around 20% (£3.16 billion) of that cost was incurred by employers and 22% (£3.5 billion) by the government. Yet the majority of these costs (59% or £9.56 billion) fall upon the injured and ill individuals themselves.
The data also suggests that many people are going into work when sick or injured. Between 2017/18 and 2019/20, there was a 12% decrease in working days lost through work-related injury or illness. The figure dropped to 2.1 million, from 2.4 million between 2015/16 and 2017/18.
The findings, collated by Herts Tools, used construction statistics from Health and Safety Executive reports from 2018 to 2021. The analysis demonstrates the impact of accidents in the construction industry and how workers and workplaces are being affected.
Continuing to work through illness or injury can have severe, long-term consequences for physical and mental health. Physical injuries might be aggravated by carrying on with regular duties – especially if manual labour is required – causing further absences in the future.
Construction site injuries are growing in number, but both prohibition and improvement notices are becoming less common. When compared to 2017/18, 61% fewer prohibition notices were issued in 2020/21, and improvement notices were down 54% over the same timeframe. In addition, there were 63% fewer prosecutions, giving those who suffer accidents little hope of achieving justice.
Stefano Lobban, director at Herts Tools, says: “Although there will always be accidents in the construction industry, we can never stop trying to reduce them. These latest findings show just how far we have to go, with the cost of workplace injuries rising relentlessly, despite the UK having some of the most thorough health and safety regulations anywhere.
“Training is key to protecting workers, whether it’s highlighting dangers or teaching workers to make their own risk assessments on site. Then there’s ensuring workers have all the PPE they need, such as helmets, safety goggles and slip-resistant footwear. Workers should also be encouraged to be honest about their health and not risk their future wellbeing by working on through injury or illness.
“I hope these findings act as a wake-up call to the industry and we’ll see a reduction in incident numbers next year.”
Phil Beaumont, Health and safety consultant, says: “First and foremost, it’s important for sites and companies to implement rules, procedures and policies that people can easily follow to stay safe at work. Minimising future accidents also depends upon keeping a record of incidents and continuously assessing what went right, what went wrong, what was irrelevant and what more could have been done previously.
“If a company reports an accident at work concerning one of its workers – depending on the severity of the accident and cause – they should carry out a thorough risk assessment for the returning person. This ensures they’re capable of doing the tasks they’re assigned and won’t aggravate their recovery. This should also include manual handling and Control of Substances Hazardous to Health (COSHH) assessments.
“It’s also worth looking at a buddy system, temporary assignments, reduced hours or planning a stepped return to work for the injured party.”
How can companies prevent accidents on site?
- Provide training and plan all work at height properly
- Use the correct equipment and regularly check it to prevent falls
- Avoid slips and trips by keeping floors clean, dry, well-lit and free of obstacles
- Clear up spillages quickly, deep cleaning after working hours
- Install safety guards on machinery and provide safety goggles
- Store heavy objects close to the ground, fit debris nets and outlaw throwing tools
Read the full report here