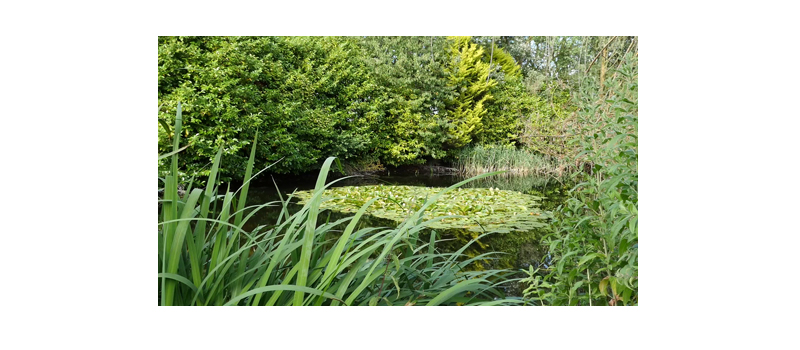
Keith Clarke replaced his gas boiler with a Kensa 24kW Single Phase Twin Compressor to harness heat energy from a nearby lake to provide space heating and hot water to his Grade II listed farmhouse.
Watch the video case study here: www.kensaheatpumps.com/video.
Mr Clarke and his family recently moved into River House, a spacious Grade II listed farmhouse in Cambridge. They discovered that their new home was heated by a 20 year old mains gas boiler which struggled to keep the house up to temperature and was expensive to run.
Keith was familiar with ground source heat pump technology and knew it was an environmentally friendly choice that would eliminate reliance on fossil fuels. He approached experienced Cambridge-based renewables installer Cernunnos to talk about designing a ground source system that would meet the family’s heating and hot water needs.
In the initial consultation, Cernunnos recommended Kensa Heat Pumps as a preferred supplier of ground source heat pumps, because its models are manufactured in the UK and also because the Kensa 24kW Twin Compact, the largest single phase compressor on the market, was best placed to handle the property’s high heat load.
Harnessing heat energy from a natural water source
River House has a large lake on the grounds which is fed by a natural spring. Cernunnos measured its flow rate along with its area and depth, and provided this information to Kensa, which recommended that the Clarkes use the heat energy in the lake for their heating and hot water. Water is an excellent conductor and has a higher heat transfer rate than the ground, with the return temperature to the heat pump being generally 5-6°C higher than ground collectors. The fact that the water in the lake is in close contact with all of the pipe at all times and has the spring constantly replenishing the energy in the water further enhances the efficiency.
The team from Cernunnos sunk five specially created Kensa pond mats consisting of 300m of slinky pipe attached to weighted and corrosion resistant stainless steel frames to the bottom of lake. They connected the closed loop system up to the heat pump which is housed in an annex building via pipes running under the lawn up to the main house. This method removed the need for large amounts of drilling or digging, thereby reducing the cost and duration of the installation.
The challenges of working with a Grade II listed property
Due to the fact that River House was a Grade II listed farmhouse, Cernunnos needed to ensure that the energy efficiency of the property was considered and improved where necessary. The less efficient the property, the greater the heat loss, which would result in a bigger and more expensive ground source heat pump and associated running costs to maintain temperature in the home.
Cernunnos undertook a detailed heat loss study at the start of the project which showed that the house had previously installed basic insulation measures to improve its heat loss. However, the annex building was poorly insulated. Cernunnos therefore installed extra insulation underneath a suspended timber floor using 100mm rigid insulation between and 25mm below the rafters, as well as adding loft insulation.
The study also showed that many of the existing radiators were already oversized and simply needed upgrading from single to double panels. Oversizing radiators ensures that they will work at a lower flow temperature, thus reducing the amount of work the heat pump is required to do to ‘uplift’ the renewable heat energy from the ground to the required temperature for the home.
Peter McKeown, Director at Cernunnos said: “We also installed underfloor heating in some rooms downstairs, which works well with the ambient temperature delivered by the heat pump, which, together with the new radiators, ensure an efficient installation all round. We also recommended that the Clarkes use state of the art Honeywell Evo-Home heating controls to allow them to control the temperature independently in every single room.”
In the vast majority of cases, planning permission is not required when installing a ground source heat pump. However, as River House is a Grade II listed building, the Clarkes had to seek permission for the installation and the upgrades to the insulation and heat distribution system. In this case the local authority planning department was very supportive throughout the process and permission was granted without a problem.
Chris Davis, Commercial Director at Kensa Heat Pumps, said: “More and more people are realising that they can use water as a heat source for their ground source heat pump as it is an excellent conductor. In this case, the Clarkes’ lake has a natural stream flowing into it, replenishing the energy supply and creating a highly efficient water source system.
“The property had a high heat load on a single phase power supply, so Kensa’s 24kW Twin was perfectly placed to provide the required levels of heating and hot water. The measures that Cernunnos took to improve the heat loss of the building, taking into account its Grade II listed status, meant that the Clarkes benefit from lower running costs too.”
Saving money through system efficiencies and Government grants
Mr Clarke said: “I knew that ground source was a great technology for extracting the natural heat that’s available from the environment to provide a completely green heating system. The good thing about the pipes being in the lake is that water has great conductivity, meaning we are able to extract heat sustainably throughout the winter to keep the house perfectly warm.
“I know that there’s a big investment involved in getting a ground source heat pump, however we realised that we could get the whole thing paid for with the Renewable Heat Incentive, including the installation. Plus, we’ve ended up with a system where the yearly cost of electricity is less than we would have been paying for gas.”