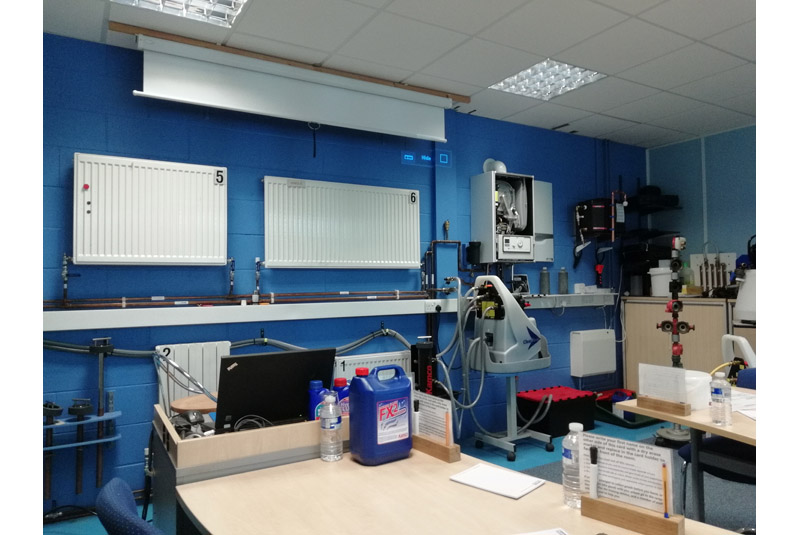
With a greater emphasis on efficiency, combined with the introduction of modern boilers that are more susceptible to corrosion deposits due to intricate components, powerflushing is fast becoming an increasingly necessary skill for installers. PHPI attended a one-day training course with Kamco to find out more.
The importance that Kamco places on powerflushing and supporting its installers became immediately apparent in early March. Despite the worst of ‘Snowmageddon’ hitting, the team based at the company’s St. Albans headquarters were determined to go ahead with the course – as were a number of installers who braved the Siberian weather – making it clear the importance they too, placed on understanding this key skill.
Nor was Kamco’s Trainer, Giles Hanford, to be put off. Diving straight in to the one-day course, he was quick to highlight why powerflushing is necessary – and more than ever. Ultimately, doing it correctly should ensure a more efficient and healthy heating system, eliminating cold spots on radiators and clearing pipes blocked by solids such as magnetite and rust. What’s more, with modern boilers more susceptible to corrosion deposits due to their smaller, more delicate parts, many manufacturers will insist on the process before installing a new unit to uphold the warranty. It’s no surprise then, that more powerflushes are being carried out by engineers than ever before.
The fact that many installers also run their own businesses was not missed. “At the end of the day, as an installer you’re responsible if a boiler fails after installation,” says Giles. “While I would never recommend powerflushing for the sake of it, it’s important to be able to explain to a homeowner why it’s necessary, particularly when replacing an older system. It will help protect the new boiler and maintain its warranty, while resulting in additional revenue and fewer callbacks for the engineer.”
As Giles ran through this reasoning, he engaged the participants around the room, keen to understand the various levels of experience in attendance. More experienced installers will likely have run a number of flushes before, and were often open to discussion on their different experiences and solutions they have found to combat any problems – adding value to those less experienced. Throughout the day, which runs from 10.30 to around 4pm, every participant had learned from the course, as well as each other – an aspect Giles actively encourages.
Flush point
While theory is crucial to a greater understanding, the key to the course from Kamco is the live running of a powerflush during the day on a neat, and easy to follow pre-arranged setup in the training room. After outlining the principles of assessing a heating system before running the process, breaking up sludge with chemicals – such as Kamco’s FX2 – and warming up the system to increase the speed of reaction, it’s time to begin the flushing process.
“The live demonstration enables active participation from the attendees, which should give them more confidence when they leave the session,” adds Giles. “Showing the connections and details of a standard machine is all well and good, but getting the installers out of their seats to maintain the water levels, reverse the flow and dump the dirty water adds another level of understanding to the day.”
The demonstration begins from late morning and covers the majority of the time remaining – running throughout a break for lunch. Giles is constantly explaining what’s going on in the system, while simultaneously asking participants questions on previous experiences to demonstrate the different situations engineers may find themselves in. While it may feel a little fast-paced at times, he rounds up the entire process at the end of the day, as well as running through a series of FAQs – turning what can at first seem a complicated process into a simple one.
As one attendee commented: “There’s a lot to take in on the day, simply because so many situations are covered. The theory and summary gives a great overview, however – you come to realise that the principles behind each system are the same, they just need to be adapted to suit the job you’re working on. The process now feels a lot more ordered when explained like it has been.”
Not just content with knowing how to run the powerflush, Kamco also makes certain installers know when the process is complete, including advice and practical experience of using test. Levels of clarity, purity and pH are all tested to make sure the flush has done its job properly, with additional advice on how to combat any further problems at this stage – such as adding neutralising crystals to remove remaining acidity.
There’s a number of key takeaways from the day, perhaps the most important being that no two powerflushes are likely to be the same. As an engineer, it is crucial to check the heating system before beginning the process – powerflushing won’t break metal or cause a fault if done correctly, but it will find existing problems as water rushes through at a high flow rate.
Continuing this theme, Giles runs through a number of different systems to close the day, covering everything from combi boiler systems to microbore and single pipe. Kamco also ensures installers know which systems not to flush and offers advice on inhibitor selection.
Throughout the day, debate was encouraged in a comfortable, relaxed atmosphere – while Giles expertly covers a wide variety of scenarios installers may come up against. As a consequence, whatever experience you may have with the process, Kamco provides an excellent overview of the necessities, principles and skills needed to run a powerflush – with plenty of biscuits on offer throughout!
Click here for more information on the training courses on offer from Kamco.