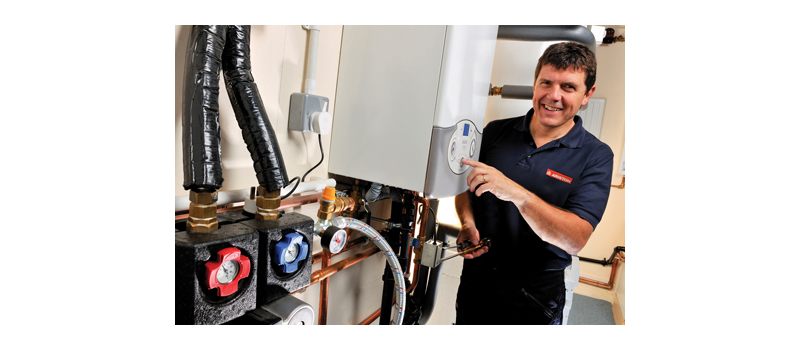
The UK boiler market is looking healthy for 2015, but it is important that installers keep up to date with the latest product developments and advances in heating technology. Alan Hayes, Technical and Quality Manager at Ariston, discusses the importance of boiler training and its role in growing installers’ businesses.
We are all well aware that boilers and cylinders need to be maintained to ensure they remain in optimum working condition. All appliances should be serviced annually, so installers need to keep their product knowledge up to date, both to preserve servicing standards and keep customer satisfaction levels high.
Of course, heating technology continues to evolve and, with over 20 million boilers fitted throughout the UK, installers need to invest in training to remain on top of the latest product advances. Plus, there are alterations and additions to legislation and regulations – knowledge of which is equally as important as understanding how to fit and service the technologies available.
The recent report by the Confederation of British Industry (CBI) – Engineering Our Future – quoted a CBI/Pearson survey showing that last year 42% of firms faced difficulties recruiting individuals with science, technology, engineering and maths (STEM) skills and knowledge. The same CBI report quoted a number of studies which similarly anticipate an increase in skills shortages over the coming years. Findings of this nature should not be ignored, as while the heating industry is gradually recovering from the economic downturn, it would be unfortunate to be let down by a lack of skilled workers.
The UK Government announced in its last Autumn Statement that, from April 2016, it will make it cheaper for employers to take on an apprentice by abolishing employer National Insurance contributions for apprentices aged under 25. This is good news for the heating industry, as it is encouraging the heating engineers of today to educate the next generation, but there is still so much more that can be done.
Heating manufacturers should be contributing towards providing existing and future installers with the skills required to grow their businesses. At Ariston, we have already invested in a network of UK training centres, as well as a display and training vehicle (DTV), which offer free high efficiency gas boiler courses. These offer theory sessions and hands-on, practical classroom experience – including expert tuition on understanding the operational parameters, such as how to range rate the boiler and install a multi-zone system. As a result, engineers who attend are able to obtain valuable experience with live gas and water connections, as well as become familiar with the latest products and technology – plus understand the relevant legislation they fall under. Delegates also receive £300 cashback (subject to terms & conditions) upon attendance, so it also makes financial sense to keep up to date with training.
It goes without saying that any course installers attend needs to be industry recognised, covering all aspects of specification and installation, from boiler positioning to servicing, maintenance, commissioning and fault finding (including understanding any product specific fault codes). Constantly raising their standards not only enables installers to enhance their skillset, they can also bolster their profitability by being able to fit and work on a greater array of products for a wider selection of customers. In addition, those armed with the latest industry knowledge and trends will be able to stay one step ahead of their competitors.
Boiler training also provides installers with a thorough understanding of the importance of servicing, while encouraging them to make customers aware of gas safety. Training programmes will educate gas engineers on how to check combustion settings and correctly use a flue gas analyser to measure CO2 levels, as well as check other elements such as boiler efficiency, data logging and differential pressure.
Manufacturers’ training courses will also outline how to inspect, clean and/or position a flue safely, as well as check condensate traps and other hot water-related and servicing issues, such as calculating temperature rises and measuring the flow rate. All relevant documentation should also be explained; for example, the HHIC Benchmark Commissioning List, which is supplied with every boiler in the UK and validates the installation warranty.
Furthermore, from a customer’s perspective, a well-trained, qualified gas engineer is reassuring to them, as any work is being carried out will be to the latest and highest standards, which can only be in their best interests. Training and certification is the best way for installers to convey trust to clients – after all, they don’t want to hire someone who doesn’t know what they are doing. Plus, the more trained installers the industry has, the better its reputation will be, while it should significantly reduce the number of ‘cowboys’ carrying out substandard (and often illegal) work.
Installers will undoubtedly have boilers they recommend and fit on a daily basis, but they still need to have a full working knowledge of every connection and product function to guarantee a safe, straightforward and professional job. Training is a valuable asset – and the old adage “train to gain” is true; not only does it ensure all work is conducted safely and in line with the latest industry legislation, it is an essential requirement for heating engineers and companies seeking to grow their businesses.