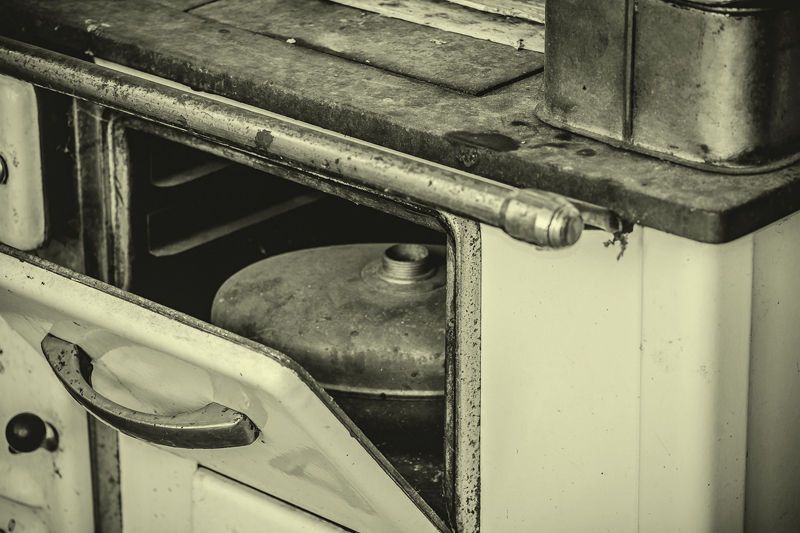
Given that there is a buoyant market for antique and reconditioned solid fuel burning and oil fired stoves, John Thompson, APHC CEO, looks at what potential implications could arise from fitting such appliances and ensuring they are ‘fit for purpose’.
It is important to note at this stage that ensuring the appliance is ‘fit for purpose’ is separate from the installation requirements under Part J of the Building Regulations.
Since 1 July 2013, any new solid fuel or oil burning appliance is required to have a CE mark under the Construction Products Regulation. The manufacturer and supplier are responsible for ensuring they only supply new stoves which meet the European safety and efficiency standards, which the CE mark demonstrates and guarantees. This is important because if an installer is supplying the appliance, then he or she is therefore responsible for ensuring the appliance complies with the European safety and efficiency standards – that is to say, the installer is responsible for ensuring the appliance is ‘fit for purpose’.
This isn’t an issue for new stoves as an installer simply needs to ensure the appliance carries the CE mark. However, there is a market for antique and reconditioned stoves, many of which were originally placed on the market ‘as new’ prior to the 1 July 2013 and so won’t carry the CE mark.
Having the CE mark isn’t applicable to antique appliances due to their age as they are not sold ‘as new’ and the Construction Products Regulation does not require retrospective application. If a stove does not carry the CE mark then enquiries with the supplier and (if applicable) manufacturer should be made to ensure that it was originally placed on the market prior to the 1 July 2013 and that it isn’t a non-compliant new product.
It is a legal requirement for the installer to ensure the stove being installed meets the necessary requirements of British and European standards. It is perfectly legal to install antique and reconditioned stoves providing the installer can demonstrate and document that the installed stove has been safety tested and meets British and European standards and minimum efficiency standards.
In order to be able to do this, the installer needs to ensure that the supplier or the customer – should the customer have purchased the reconditioned stove – is able to supply written documentation detailing what refurbishment work has been undertaken and that the stove has been safety tested and complies with all relevant legislation and efficiency standards.
In addition to the restoration and safety test documentation, the installer should ensure the stove includes the manufacturer’s original installation documentation. If the stove doesn’t have the original manufacturer’s documentation, then the installer should attempt to obtain them either via the internet or by getting in touch directly with the manufacturer.
The installer should then follow the manufacturer’s installation instructions unless, due to changes in regulation, they now conflict with Part J of the Building Regulations.
If the manufacturer’s installation instructions are unavailable then the installer will need to obtain further written confirmation from the supplier or customer that confirm that the implementation of relevant tests has been carried out that confirm the appropriate fuel(s) for usage, the stove’s efficiency performance, heat output etc.
If the installer isn’t able to obtain written documentation regarding the refurbishment work, safety testing, usage instructions and installation instructions, then APHC strongly recommends for the installer to not install the stove as it could be the responsibility of the installer to demonstrate that at the time of installation the stove was safe and efficient, that appropriate materials and components were used during refurbishment, and that the installation complied with the requirements under Part J of the Building Regulations.