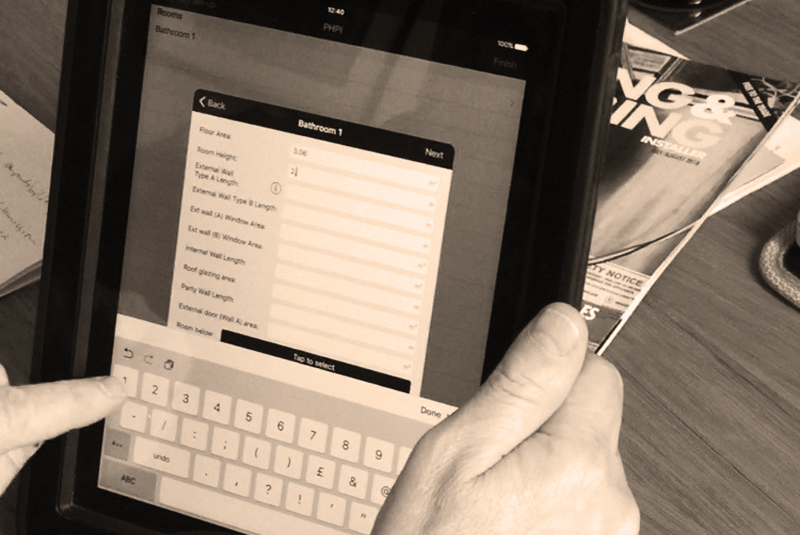
Rob Berridge asks why there isn’t more joined up thinking in the heating industry.
If you are anything like me and have completed over 50 laps around the sun, with most of that time spent within the UK heating industry, you will undoubtedly have many theories of how we should best move forward into 2019 and beyond.
Indeed, most of the engineers, specifiers and ‘industry support crew’ I meet and speak to on a regular basis say exactly the same things:
- Where is the joined up thinking in our industry?
- Where is the expert guidance from our governing bodies?
- Where is the cohesion that should link governors, manufacturers, suppliers and installers into that unbreakable, cooperative chain?
It appears that we have ‘virtue signalling’ incentives for this, controls for that, meters for that, filters for this, blah, blah, blah – when in fact, we are making the cardinal mistake of again treating the symptoms of our problems whilst not addressing the real cause.
What is the cause?
The largest number in science is called a ‘Graham’! Yep, I laughed too and they possibly could have thought of a more original name (sorry, Graham) but to answer the above question is ostensibly akin to this as problems within our industry are so vast and should be debated during further laps around our sun, I guess?
However, every renewable, every boiler, in fact every possible need for the source of heat comes under the exact same requirements and proven rules to run efficiently. This is the process of calculating building fabric heat loss! How we heat our buildings is irrelevant to this discussion but how we calculate and specify the heat source is absolutely everything.
We seem to have sauntered rather blindly into a ‘rule of thumb’ form of measurement and specification which, as an engineer, I want no part of. The ‘guesswork’ of boiler and plant sizing has caused an estimated 90% of all UK plant to be vastly oversized, causing a cumulative and devastating effect on our climate, our utility bills and system component failure.
As engineers, we know that running any engine at peak revolutions, or loading and unloading, will shorten the life of the said unit and completely destroy its efficiency and longevity. This may explain why vehicle mechanics continually ‘fettle’? Fantastic if you are a petrolhead and are lucky enough to blast around a track in your favourite equation of wheels but disastrous if you are a stallion 30kW boiler wrongly installed into a two bedroom flat. No matter how much you fettle the boiler, if it’s too big, it will never be efficient.
A recent heat loss calculation, carried out on my own three-bed Victorian terrace, resulted in a mere 4.76kW of heat loss through the building fabric. Admittedly, I have refurbished my property with new efficient windows, insulated the floors and roof voids – but the solid walls remain. I must admit also that I was shocked at the result but had faith in the science and set about hydronically balancing and adjusting the heat curve and output on my boiler to match the calculated requirement. The result of these small changes has shown a vast reduction in gas usage and yet my property maintains a very comfortable 21°C.
I have refrained from wanting to publish the above until I had utility bills to back up the hydronic experiment but the word is out; We have got it so wrong for so long!
We can do so much more and indeed, my boiler still cycles somewhat because one simply cannot turn it down far enough.
The best-selling air source heat pumps in the UK are around 10 or 12kW and yet the best-selling gas boiler is a 30kW unit. Strange that these proverbial dots are not joined up?
Boiler manufacturers have two options, in my view:
- Make smaller boilers in 6, 8, 10 and 12 kW options
- Manufacturer heat exchangers that can modulate to extremely low flow rates but still demand low fire and maintain delta T.
We also must lobby government to update Building Regulations to incorporate accredited heat loss calculations into the planning process. This will work alongside the current, theoretical only SAP and ERP reports. The final icing on the cake would be building performance testing under full heat load with calibrated thermography imaging.
Only then can we accurately state that we have buildings worthy of the hundreds of thousands of pounds that we fork out over 30 years or so. We would also then be in the enviable position of top rankings in engineering efficiency and value for money.
Having just got over the Christmas period, I was examining some of the gift packaging given to the various children of friends and neighbours. It is both amazing and shocking that a little teddy bear goes through a plethora of testing worthy of a pre-flight space mission; a new car is performance tested and safety tested to oblivion and yet our biggest purchase in our lifetimes (our house) gets ‘diddly squat’.
We all know that we get so much wrong in our building industry but is it really too much to at least expect that our minimum Building Regulations are applied and enforced, calculations are done and proper performance testing is correctly administered? No, I didn’t think so either.
About the author:
Rob Berridge (EngTech MCIPHE) is a commercial and domestic heating engineer with over 35 years’ experience in the industry. He has been a heating design consultant for the last five years and is the director of Heat-Engineer.com and Rob Berridge Plumbing and Heating Ltd, to which his design consultancy is attached. Rob is extremely active in promoting engineering best practice within the wider industry and seeks out the likeminded for this cause.