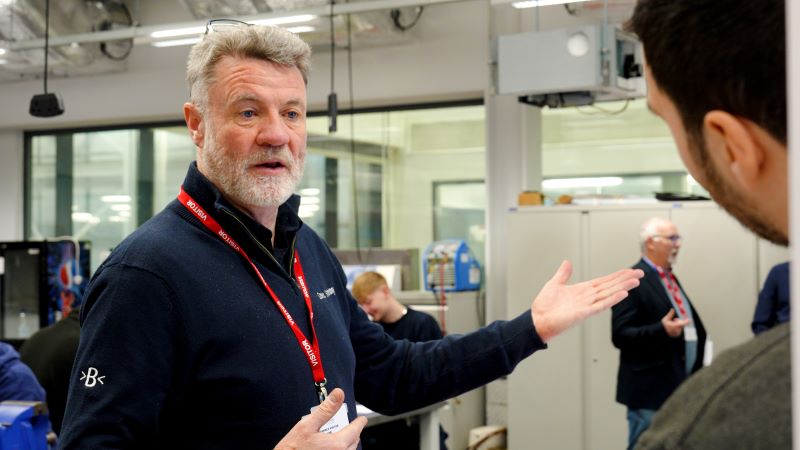
Conex Bänninger has collaborated with Dudley College of Technology to provide training in the installation of the >B< MaxiPro, a press-fit range of copper fittings: the system is designed with a 3-point press system (up to 1 5/8”) to provide a permanent leak-free joint.
A series of training sessions were recently undertaken by Mike Lucken (pictured), Technical Sales Manager – ACR for Conex Bänninger and delivered to apprentices studying for the three-year Refrigeration Air Conditioning and Heat Pump Engineering Technician – Level 3 qualification.
College Lecturer Chris Clamp commented: “All the apprentices are currently working in the RAC ‘field’ and attend the course once a week through day release, whilst at work for the remaining four days. The course focuses on the practical skills and knowledge required to install, service and maintain refrigeration, air-conditioning and heat pump systems. During their time at the College, they also obtain the F-GAS certificate, which allows engineers to work with refrigerants.
“I first became aware of Conex Bänninger after seeing an RAC webinar and subsequently invited them to provide training to our apprentices.
“Press fit is ideal for new-build projects, with lots of work currently taking place in schools and colleges in London, for example, and a significant number of these builds don’t allow brazing – as no hot works are permitted ‘on-site’. Press fittings are also a lot quicker to install and don’t need a permit.”
Darwin Siooito is undertaking an apprenticeship with AGGORA, the nationwide commercial catering solutions provider that employs both catering equipment engineers and refrigeration engineers. He commented: “The Conex Bänninger training session was informative, and we were able to learn about the whole process of installing the >B< MaxiPro. Installation is quick and easy and faster than brazing. The training session was very good.”
Mike Lucken commented: “One of the biggest challenges facing the HVAC industry is a skills shortage and that is why so much of my time is spent training apprentices up and down the country about press fitting. Whilst plumbers and heating engineers have been working with press fit since the 1980s, there is still a need to make engineers in the air conditioning and refrigeration industry aware of the advantages that press fit offers over established jointing methods such as brazing.
“The apprentices at Dudley College of Technology had the opportunity to try their hand at installing >B< MaxiPro fittings. Choosing the correct tube for a job and cutting to size with a proper pipe cutter is essential. The tube then needs to be deburred inside and out to ensure no debris is left in the pipework and that it has a smooth finish. The next step is to use a depth gauge or the fitting socket to mark the insertion depth, simply insert the tube in the gauge or fitting and mark the depth of the tube with a marker pen. This gives a visual guide that the tube is fully seated in the socket at the correct depth.
“Once the tube has been marked to the correct depth, take the fitting and put it into the jaw. Press the joint using a press machine to achieve the perfect joint then mark the fitting to so that the fitting can be identified as being pressed.”