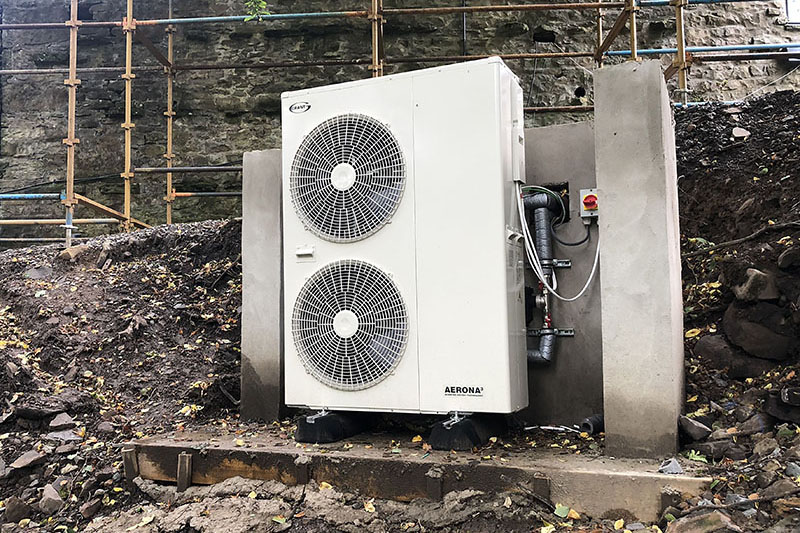
PHPI follows the renovation of a farmhouse on its journey to be carbon neutral.
In 2019, following years of minimal maintenance, a 300-year-old Yorkshire farmhouse was purchased by new owners who started a major renovation project to extend the property and make it more energy efficient. During the renovation, the ground floor has been completely re-built and a new roof has been installed, elements of the renovation which enabled the insulation of the property to be significantly improved, helping to reduce heat loss.
An environmentally friendly ethos was at the centre of the project so selecting a renewable heating system was an easy decision. “Throughout the renovation, we were keen to make the building as energy efficient as possible,” commented the homeowner. “Installing an air source heat pump was the natural choice to replace the oil heating system that previously heated the property. We have been advocates of reducing our carbon footprints for many years and, through my work, I have learnt a lot about renewables from Grant UK so when we started this project, I was keen to put the theory into practice.”
Efficient system
The farmhouse now extends over 250m² between two floors and the heat source of the property is a Grant Aerona³ 17kW R32 air source heat pump. Grant heat pumps use R32 refrigerant which has a global warming potential which is 70% lower than other refrigerants such as R410a. Furthermore, as it is a single-component refrigerant, R32 gas has no temperature glide which helps the heat pump operate more efficiently.
This feature of the Aerona³ heat pump was one of the reasons why it was selected for this install as the homeowners were confident that the heat pump would work as efficiently as possible while modulating the output to meet their heating demands.
Working alongside the heat pump is a Grant MonoWave high performance 400ltr indirect hot water cylinder. With a larger internal coil, the cylinder can effectively transfer heat from the system into the water ready to supply and meet the hot water requirements of the property. The homeowners decided to install the largest cylinder model we could so they can store the water very efficiently by having a low storage temperature.
Underfloor
Grant Uflex underfloor heating has been installed throughout the property. This wet underfloor heating system, which is embedded into the floor construction, comprises of 16mm pipe which has been laid in a mixture of pipework patterns – bifular and meander – to provide even heat distribution into the occupied living space of the farmhouse on both levels. The Uflex system components all came as a kit which made things easy.
After the Uflex pipework was laid, stapled and secured into place, a Topflow AFD fast drying screed was poured over the top with approximately 13m³ laid in less than three hours. The particular screed used for this installation was incredibly fast drying and could be walked on the following day, allowing tradespeople to continue with other elements of the renovation project and it was fully dry after only two and half weeks, allowing the flooring to be laid.
Comprehensive support
Throughout the installation, Grant UK’s Design and Specification Team were on hand to provide heat loss calculations, comprehensive product specification, and full line drawings for the underfloor heating system.
The fabric of the property has been upgraded to be as energy efficient as possible, and its heating and hot water requirements are being met sustainably with renewables – it also has a solar PV system which will complement the heat pump’s electricity demands to further reduce the owners’ heating and hot water bills.