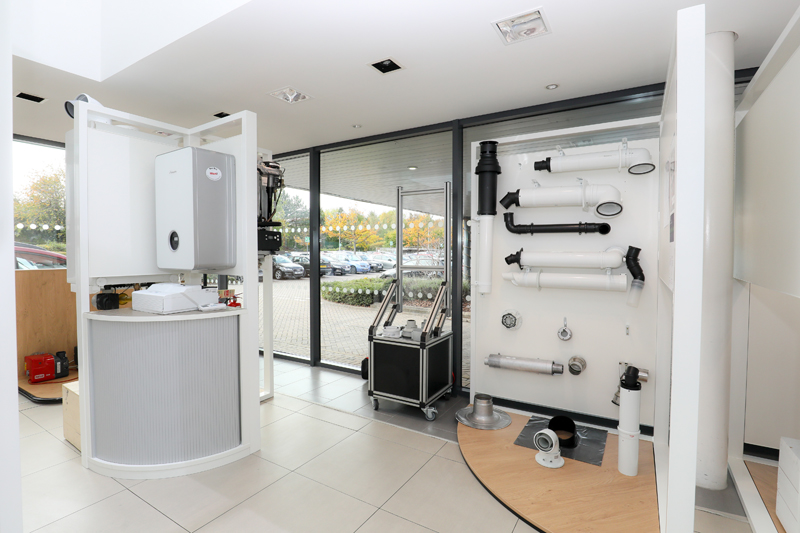
As manufacturers continue to realise the benefits of having a knowledgeable support mechanism in place for installer queries, PHPI spent the morning with the Worcester Bosch technical support team, to understand how they can help.
While it’s increasingly common practice for customer service lines to be diverted to external call centres, where hold music reigns supreme, Worcester Bosch appears to understand the importance of maintaining a reliable support network for its installer community. With over 40 technical advisors upholding a less-than 20 second average response time and taking around 500,000 calls per year, the company clearly believes this forms a vital part of its service.
Speaking to members of the team, installers will be reassured to know that almost all of them have been on the tools at some point before now. This became instantly clear as we listened in on real time calls, where many would be doing what can only be described as some kind of mime-like-act to an imaginary boiler in thin air, as they tried to work out which stage of the process their customer was describing. And, if this doesn’t work, the team are able to walk to the neighbouring showroom and literally play around with the various boiler models themselves.
Worcester manufactures a variety of different heating solutions, so the team ensures there is specialist support staff operating at all times. Some will be experts in the gas-fired models, while others will specifically deal with heat pump or oil related enquiries to guarantee all bases are covered. As well as ex-heating engineers, there are also ex-electricians and spares support staff available.
All of this means that the technical support team holds around an 80% hit rate of successfully dealing with calls, according to the business. Annual refresher training covers a wide array of different scenarios, and very often those calls that are unsuccessful are likely due to the problem being with a different issue within the system, which may not be Worcester related – i.e. a heating control or TRV that isn’t playing ball. Crucially, it is highlighted to all members of the team to not ‘blag their way’ through a call, meaning installers should expect responses to be well considered and thought out.
Sitting in on some of the conservations, it becomes clear this is the case. While some scenarios can be dealt with almost instantaneously, others inevitably take some more consideration. Worcester’s advisors have full access to every boiler and control manual that the business has manufactured over the years, but problems are sometimes best solved with teamwork, as the installer and advisor work together to solve the problem. As one engineer commented: “It’s almost like having an experienced colleague by your side, just not physically!”
Over the course of the morning, queries ranged from a timeclock issue when wiring a thermostat, to a diverter valve fault. Each call was responded to immediately, though installers may need to be a little patient during heating season, and the office is open from seven in the morning, until eight at night.
With a number of new boiler launches in 2019, there’s bound to be a few differences in installer touchpoints, so engineers should be pleased to hear that Worcester looks set to continue to place a great deal of importance on its support network at present.