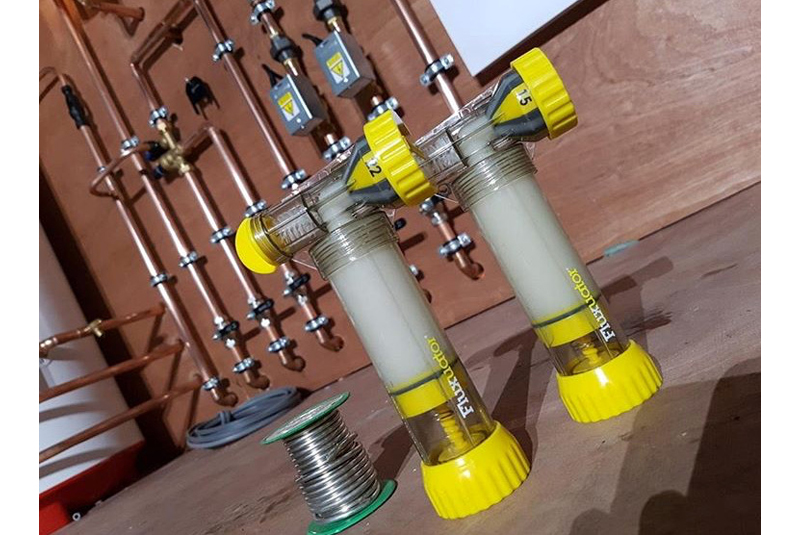
Stuart Duff puts the questions to Deborah Fowls about Fluxuator, to find out how the business started, how the product works and how it can save installers time.
Tell us a little bit about the history behind Fluxuator
Dominic is the inventor of the Fluxuator. He had the idea about 10 years ago, while working on the tools. It stayed as an idea until he had a massive heart attack in 2012 and could not work. It was then he spoke to his good friend Zach about it and they decided to bring the idea to life.
How does the product work?
It works by dispensing flux to be distributed onto copper pipe – with no waste, or contamination to the flux. By twisting the base of the tool – the manageable click system – a plunger pushes the flux up into the head unit and onto the brushes. The installer then places the Fluxuator over the copper pipe and, with a 90° turn, it coats 360° of the pipe. If the head gets dirt or debris in it, it can be washed under the tap.
How easy is it to refill?
There are refills available – so when you run out, just unscrew the empty one and screw another one back on. Although the installer could refill the empty container with flux, it is messy and time consuming. We also don’t endorse this, as the tool has only been tested with our flux in it.
What flux do you use?
The flux we use is Copalux flux; it’s a non-acidic, water soluble flux with a pH of 7 (which is neutral). It’s UK WRAS approved and is suitable for gas, hot and cold water and potable water.
Are there versions available for different pipe sizes?
At the moment there are two sizes available, 15 and 22mm. We have been asked why we didn’t make a multi head tool but we are a small company with limited funds, and tooling is expensive. It’s easy to say but not so easy to do. We will eventually bring out a 28mm, and one day maybe even the multi head tool.
Can you give us an idea of how much time an installer could save by using the product?
I can’t give you time specifics, but think of it this way; with a pot and brush, you have to dip the brush in the pot and literally paint the flux around the copper pipe. With the Fluxuator, you simply twist the tool 90° and the whole of the pipe is coated with the right amount of flux. There is also no need to unclip pipework in situ as the head of the tool has been designed to fit around the pipe without the need to remove it. Also, a couple of clicks will coat two or three pipes before the need to click again. It also saves money because there is no waste. The whole 75g container is used, and it gives approximately 500 applications. We are also currently concentrating on lowering our carbon footprint by reducing the packaging that is currently used. Plus, the refill cartridge can be recycled.
What has the feedback been like from installers?
The feedback from installers has generally been excellent; we have a lot of installers posting their work with the Fluxuator on Twitter and Instagram – not just in the UK, but in America and Canada as well. We understand we can’t please everyone, and we really do take on board all the feedback we receive from the installers, whether it is positive or negative. All we ask is that they try it. We find that, once an installer has used the Fluxuator, they love it.
To find out more visit www.fluxuator.co.uk.