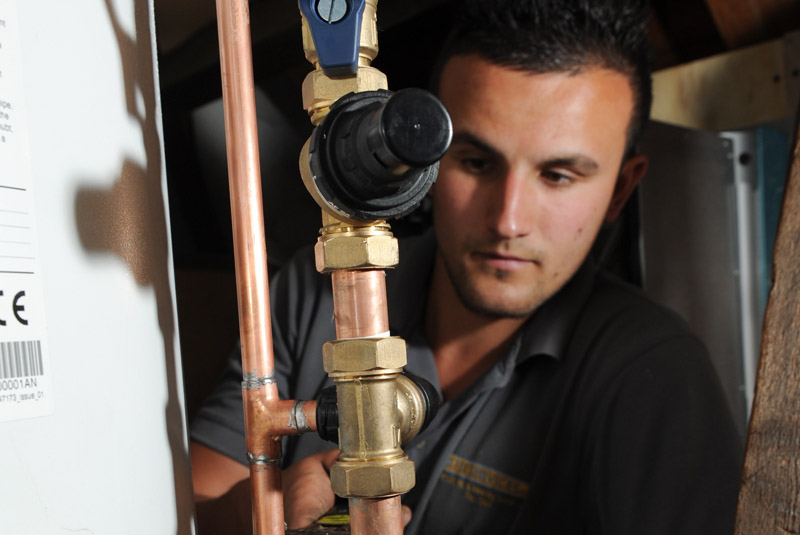
Domestic unvented water cylinders have come a long way over the years, and whilst combi boilers have become more popular in recent times, cylinders are still vital for homes with multiple bathrooms and fixtures which require fast flowing, powerful hot water supply. We spoke to Alan Clarke, Technical Support Manager at Heatrae Sadia, about the evolution of the UK cylinder market.
The landscape of hot water has shifted drastically in the last decade. Our homes have changed, both in terms of size and water delivery requirements, and we have seen a greater emphasis on issues such as sustainability.
So, how has the industry reacted to these changes, and what does that mean for the future of hot water? Alan Clarke, a key member of the Megaflo research and development team, answers our questions.
What did the domestic unvented water cylinder market look like in 1994 when the first Megaflo came off the Norwich factory production line?
At that stage, it had been less than 10 years since the UK Building and Water Regulations had been amended to allow the installation of unvented water heaters, and the products on offer were very different to today’s.
Following the change in regs, most water heater manufacturers were producing domestic unvented cylinders using copper, a material which was familiar to the UK market as it had been used in the production of vented cylinders for nigh on 100 years. However, to withstand the higher mains pressures, the copper gauge of the units had to be increased, making the cylinders relatively expensive to produce.
A number of enamelled steel units were introduced into the UK market, but were unsuccessful due to their weight and the necessity to regularly check the condition of the sacrificial anode fitted to them.
Megaflo cylinders represented the ideal solution to these issues. A pressurised cylinder which was both lightweight and extremely strong, with an excellent resistance to corrosion, Megaflo brought stainless steel cylinders into the mainstream.
Prior to Megaflo the use of stainless steel was almost unheard of in the UK, especially in domestic products. Now, almost all unvented cylinders in the UK are produced from stainless steel. Even European manufacturers that produce enamelled steel products for the European market have a range of stainless steel cylinders for the UK, which demonstrates how successful the material has been in this country.
Since then, the domestic unvented cylinder market has evolved significantly. How have manufacturers kept up with this?
As with any sector, hot water provision is constantly evolving as we work to improve our products and meet the needs of today’s installer and homeowner.
From a Megaflo perspective, we’ve had the privilege to be at the forefront of many innovative moves in the domestic unvented cylinder market. We were the first to introduce the internal expansion system to control hot water expansion, the first to introduce the ‘floating internal baffle’ to improve the longevity of the internal air volume, and first to produce units with an appliance-like external casing rather than a spray foamed insulation finish.
Megaflo was also the first to use purpose designed immersion heaters and controls integrated into the overall product design. We pioneered the use of multi-function hydraulic control sets and introduced the ‘coil-in-coil’ concept which improved the thermal transfer and amount of water heated when heating by external boiler. And, we were the first to introduce an inlet diffuser baffle to minimise mixing of incoming cold water, further improving the hot water output as a result.
From a wider perspective, the industry has had to react to the continued rise of renewable energy. Homeowners are increasingly aware of their impact on the planet, and are looking for ways to make their lives, and households, greener. In response to this, we’re seeing unvented cylinders which are able to work with renewable technologies such as solar thermal, solar PV and heat pumps.
Equally, as the footprint of the average UK home shrinks and multiple bathroom households become commonplace, the industry has faced the challenge of providing cylinders which are slimline in design, but still provide the same level of fast flowing hot water. Our Slimline cylinder is the only unit of its kind currently on the market that uses the internal expansion volume concept.
Why do you think installers still choose Megaflo?
Megaflo has the longest pedigree of stainless steel units in the UK market. We have always been seen as innovators and market leaders – improving and pioneering the use of new grades of stainless steel (we were the first to use Duplex) and improving product warranties to the point where we now give a lifetime warranty on the cylinder itself. It has excellent reliability, is easy to install, is fully approved and offers excellent performance, which is why we are still trusted by the best.
What do you see for the future of the domestic cylinder market?
The cylinder market has been under attack for many years by the growth of combi boiler use. However, in multi-bathroom properties and installations where high simultaneous flows of hot water are required, hot water storage remains popular.
Another consideration is that renewable energy sources require the facility to store energy, as its generation can be intermittent. Hot water thermal energy storage provides an excellent means to do this, and I can see this becoming an even bigger factor on the cylinder market in the future.
One of the biggest upcoming developments is smart control. Systems that can monitor and adapt the heating patterns of a cylinder to mirror users’ needs are the next big step for energy efficient hot water provision, and that will be a game changer for the market.