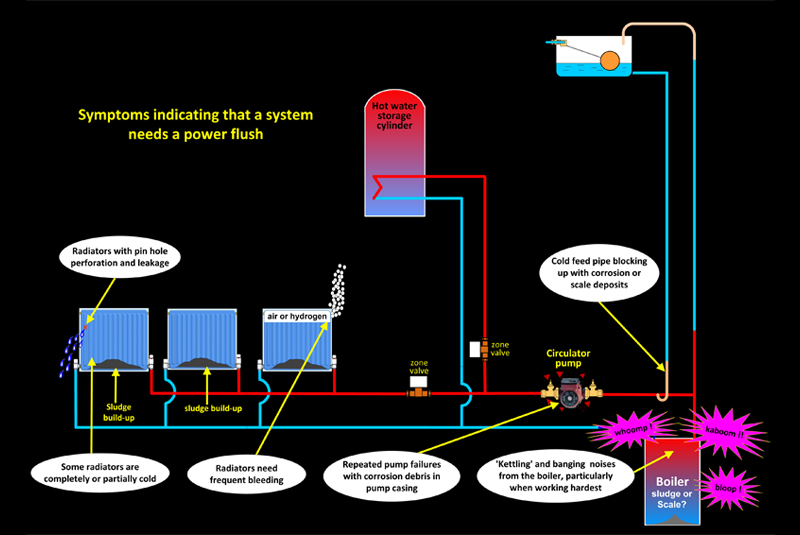
Keith MacBain, Managing Director at Kamco, offers insight into boiler longevity and knowing when to power flush.
For any installer, ensuring a boiler’s lifespan is an essential part of a job. In order to be sure that a new boiler will last a substantial amount of time, especially with the extended warranties of five, seven and even 10 years, it is essential to know when a power flush is needed, or if a quick ‘gravity’ drain and fill flush will simply do the job.
Of course, a generous warranty is dependent on the system being clean before the new boiler goes into service. More than 80% of early life boiler service calls come as a result of contaminated systems with no, or inadequate, water treatment. So for an engineer, it is clear that if you don’t get things right at this stage, the boiler is likely to have a short and unhappy life. Modern boilers are very efficient, but it is crucial that clean water is passing through the smaller diameter waterways, compact heat exchangers and critical valves. In fact, longer term debris can reduce a boiler’s efficiency by more than 15%, with proportionate increases in fuel bills.
So when would a power flush be needed?
There is no simple answer to this. Whilst engineers can’t look inside a system, there are plenty of other signs that can alert them to the need to thoroughly clean a system. These signs include:
*The system is slow to warm up.
*Some radiators are completely or partially cold when the system is operational.
*The radiators are not getting really hot even with the valves open to the maximum, but the pipe work running to the radiators is hot.
*The radiators need frequent bleeding as a result of gas generation (hydrogen gas is a by-product of the corrosion process).
*One or more radiators have failed with pinhole perforations.
*There are ‘kettling’ and banging noises from the boiler.
*The circulator pump is found to be heavily fouled and frequently needs replacing.
*Water samples taken from radiators are dirty and discoloured. If there are black particles present in the water, these will be magnetite. As this is the final stage of corrosion, large deposits can be expected within the system.
However, when drawing conclusions it is important to know that a visual inspection of water drawn from the heating system can be deceptive. The sample may appear to be relatively clear and clean, but still be quite aggressive (see Image 3). This water was from a system which had experienced five perforated radiators yet showed no iron in the solution. Use of simple drop test kits on site would reveal these problems, and at the very least the system water should be replaced with fresh clean water treated with corrosion inhibitor.
The decision of whether to opt for a full power flush or just a gravity system flush and possibly a temporarily installed magnetic filter, is for the heating engineer to decide. For peace of mind – and the integrity of a long warranty – the engineer would be best advised to power flush. In any given circumstance, and especially with a heavily fouled system, it will always remove more debris from a system.