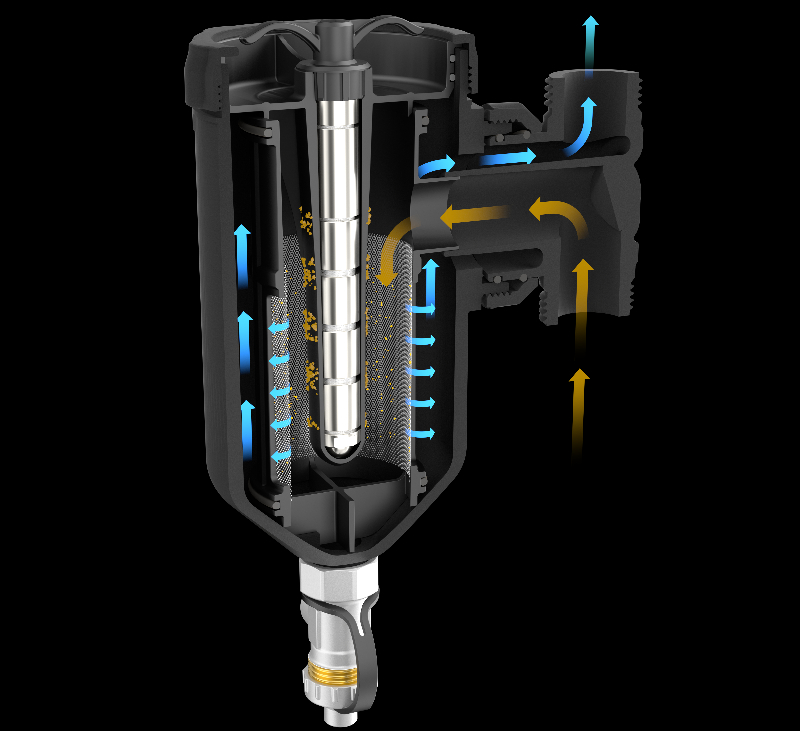
With Heat Pump systems set to become more commonplace in the future Nisar Afsar, Technical Director at Sentinel Performance Solutions, explains how to clean, protect and maintain the system water in a heat pump installation.
Like all heating systems, it’s almost impossible to have a contaminant-free system, even if it is clean to start with. As well as the usual build-up of sludge and limescale particles, other contaminants such as biological slimes and fungal growth are likely to occur in low temperature heat pump systems if they are left unprotected. The contaminants can leave the system at risk of breakdown or reduced efficiency.
Bacterial growth
A big problem that you’re likely to find in a heat pump system that you won’t find in a traditional heating system is the growth of microbiological organisms such as bacteria, algae and fungi. This is because a heat pump system operates at a lower temperature. A traditional heating system that operates at around 65 or 70 degrees doesn’t need a biocide as these organisms cannot survive at the higher temperatures. However, a heat pump system only heats the water to around 40 or 45 degrees providing the perfect conditions for microbiological growth.
Poor circulation, discolouration of the system water or unpleasant odours all indicate that the system has bacterial or fungal contamination. This can lead to impaired performance, blockages, corrosion of system components or even a complete breakdown of the heat pump system.
Treatment
So, even if there is underfloor heating and no steel radiators or copper pipework, the system needs to be treated after cleaning with an effective biocide, such as Sentinel X700 Biocide. Along with Sentinel’s X100 Inhibitor to ensure protection against bacterial and fungal contamination as well as corrosion and limescale. Just like a traditional heating system, limescale and corrosion can lead to inefficiency of the system, cold spots on radiators and noisy pipes or ‘kettling’.
Annual service
During an annual service visit, the level of inhibitor should be checked to ensure it is at the correct level to provide protection against scale and corrosion. Sentinel’s new testing kit and ‘InstaCheck’ app allows engineers to check inhibitor and water quality levels quickly on site without the need for a subscription.
Magnetic filter
The final part of the protection trio comes in the form of a dedicated heat pump filter. We all know that one of the biggest causes of breakdowns in heating systems is the accumulation of magnetite or ‘sludge’. This occurs when any steel components in the system corrode, such as radiators, pipes or heat exchangers. An in-line magnetic filter will capture any circulating insoluble ferrous particles, which can be cleaned out of the filter during the annual service.
A heat pump system differs from a traditional heating system because it uses a glycol-based heat transfer fluid. Over time, in the absence of biocidal treatment products, glycol can degrade and form a gelatinous substance that can’t be captured by a magnetic filter.
The Sentinel Vortex700 is a dedicated dual-action heat pump filter with a powerful 9000 gauss magnet that captures magnetic ferrous particles, and a high-capacity 800 micron sieve that filters non-magnetic debris, such as glycol, limescale and installation debris, out of the system. This helps to ensure that the system is working at optimum efficiency and prolongs the service life of the heat pump unit and its components.
Contaminant build-up
At some point during the life of the system, there is likely to be a build-up of contaminants for one reason or another, so using the correct additives and having a filter on the system is an effective ‘insurance policy’ to protect it against circulating debris, reducing breakdowns and prolonging the life of the appliance.
At Sentinel, we believe that part of our job is to talk to heating engineers about cause and effect: trying to correct a system that has developed problems due to contamination and corrosion is almost always much more time consuming and much more expensive than buying the additives and treating the system correctly in the first place.