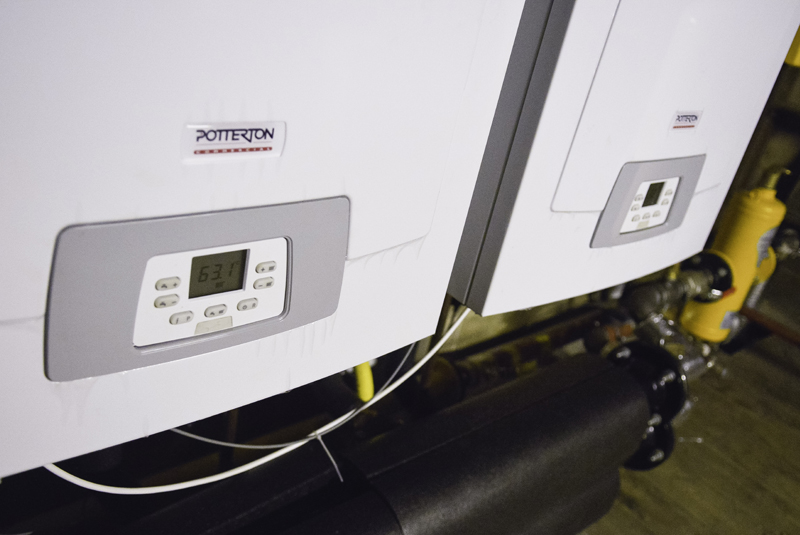
Now that ‘heating season’ is well underway, businesses are turning their attention once more to the cost of heating their premises. It’s no secret that effective energy management can have a significant impact on bottom line profit; the Carbon Trust recently highlighted that a 20% cut in energy costs represents the same bottom line benefit as a 5% increase in sales in many businesses. However, to reap these benefits, Potterton Commercial advises looking at the ‘whole life cost’ of a boiler rather than just the initial purchase price. National sales manager Steven Evans explains more.
It is easy when managing the heating and facilities for businesses to focus on the capital costs tied up with initial procurement, especially when budgets are tight. However, operational costs need to be considered too; especially when they can help the business reduce overall expenditure.
This is where whole life costing comes in. In costing out the expected life of a piece of equipment, for example, a boiler, the total costs to the business are considered and accounted for. Whole life costing should include a review of anticipated energy usage, installation costs, maintenance and servicing costs, in addition to the initial cost of the item. Then you can set an accurate, realistic budget for the products operation, maintenance and repair. And, crucially, decide whether investing in one type of product could save money over time.
Taking a boiler as an example, there are whole life costing models available that enable businesses to predict how much energy the boiler will use, how much carbon the boiler will emit, and how much it will cost to run. This means that contractors and facilities managers can make informed recommendations about the products available. For instance, through costing out the life of a boiler, there are times where a higher capital cost can lead to reduced operational costs overall.
Condensing boilers can achieve over 90% thermal efficiency compared with 70 to 80% with non-condensing models. Replacing a non-condensing boiler and updating controls can save up to 25% of energy costs, depending on consumption. A fast indication of efficiency is to review how seasonally efficient the boiler is as this gives an accurate indication of the energy efficiency and environmental impact of a system over the entire year.
Another consideration is the boiler’s modulation range. Put simply, a boiler’s modulation is the difference between its maximum and minimum output, normally expressed as a ratio. For example, Potterton Commercial’s Sirius two boilers have a modulation ratio of 9:1, which means that the 90kW model can modulate down to 10kW. A wide modulation ratio is particularly useful for premises with varying demands, as the boiler can modulate its output accordingly.
Maintenance is also important, when considering whole life costing of a boiler; ‘heating costs can increase by 30% or more if the boiler is poorly operated or maintained.’ A lack of maintenance and regular servicing can result in a shorter life-span for the boiler, as well as inefficient heating for the business and higher costs.
A boiler manufactured from good-quality materials and components may have a higher purchase price. However, it should require fewer spare parts and repairs as well as being more energy efficient and cost-saving; reducing the payback time.
Procurement based only on initial product costs do not always pay off in the longer term and we would encourage whole life costing to be carried out on all significant business investments, such as boilers. It’s better to invest in good quality products and stay warm for many winters to come.
For further information or advice on boiler specification, visit: www.pottertoncommercial.co.uk