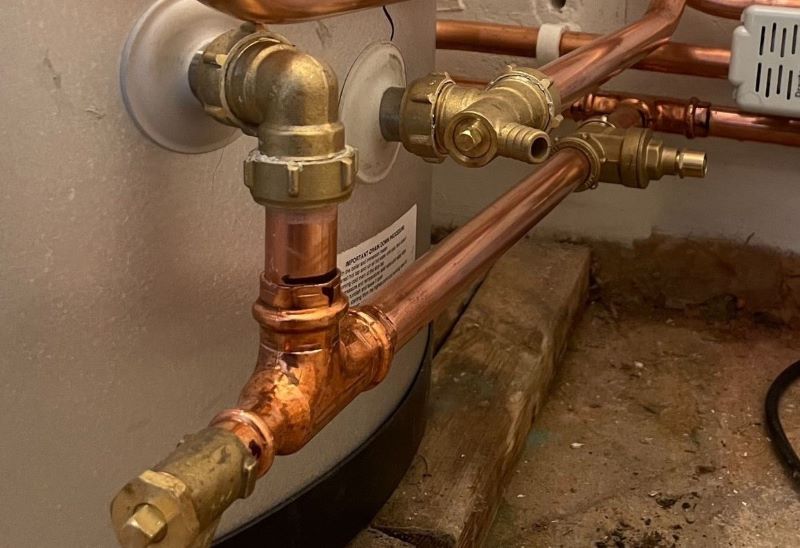
With an array of fittings available in the marketplace, what factors do installers take into consideration when selecting for a given application? Ged Grimes, UK and Ireland Business Unit Director for Conex Bänninger, takes a look at the evolution within the sector and what is driving it forward.
Traditionally, brazing was the main method for joining pipe. However, over time practices evolve and new trends have emerged. Legislation drives forward many of the changes that take place within our business including good working practices and health and safety initiatives.
Over the past decade we have seen something of a transformation within our industry and there are four main factors responsible for this. The first of these is Health & Safety regulations, which are essential to ensure the safety and compliance of installations. Within these directives is an onus on installers to stay updated on relevant legislation and codes governing pipe jointing practices. Health and Safety protocols have had a major impact on brazing practices, particularly when it comes to on-site working within confined spaces such as lofts or under floors. Increasingly, new build developers, for example, are moving away from brazing.
The second of these major influences is that of manufacturer instructions – these play a crucial role in guiding installers on the correct installation techniques and materials for pipe jointing. By following these guidelines, the reliability and longevity of the joints is ensured, whilst minimising the risk of leaks or failures.
Third, is the drive for sustainability and the need to reduce embodied carbon within building developments as well as – wherever possible – utilising products that can be recycled.
The development of sustainable supply chain management plays an important part in this and, involves using suppliers who undertake eco-friendly practices.
There is now a fourth factor: clients consider the usage and application of a product and the impact certain materials have on the environment. Safeguarding the planet is important to them and, wherever possible, use materials that are fully recyclable. Jointing methods such as press fitting and compression help minimise waste and energy consumption, thereby contributing to sustainability ambitions.
Pipe jointing solutions include…
Press-fit
Over the past decade, press-fit has become increasingly popular driven largely through a combination of legislation and the advantages that it brings to the installer including speed of installation, which can save time and money on a given project.
Unlike brazing, a hot works permit is not required for when on-site, or the need to complete a fire-watch.
Our innovative ‘flame-free’ product offerings include >B< MaxiPro for air-conditioning, refrigeration and heat pump (refrigerant) applications; as well as >B< Press for water applications and heating and ventilation applications. Both feature an innovative 3-point press which adds a layer of security and peace of mind that joints will be pressed correctly. Press fittings also offer a fast installation time of five seconds and repeatability with each joint.
Press-fit is ideal in applications where there can be flammable materials stored in certain areas. Such sites may include hospitals and airports.
The initial cost of the product and tooling kit can be quickly recouped due to the additional productivity press-fit delivers. Conex Bänninger is on a mission to create a new generation of certified installers, as well as introduce experienced installers to it.
Brazing
Many traditionally trained engineers continue to favour brazing, which is second nature to them.
Joining pipes by melting a filler metal such as brass or copper achieves strong, permanent connection, and is ideally suited to industrial piping and HVAC installations. Brazing is resistant to vibration and performs well in high-pressure and high temperature applications.
As mentioned earlier, drawbacks to this process include the need for a ‘hot-works’ permit and a firewatch following the work being undertaken.
Compression
Compression fittings are a mechanical joint providing strength, grip and effortless engagement without the need for additional sealant. Conex Bänninger launched its designed rib-nut, which is tightened by a compression spanner, in the 1950s. It is manufactured from high-quality brass materials and is used on a wide variety of domestic and commercial applications including hot-or-cold drinking water, heating, solar and gas. It remains to this day a popular choice among installers.
Like press-fit, no hot-works is required.
Push-fit
For those who are looking for an alternative to soldering, brazing or welding, and want a cheaper option to press-fit, then push-fit is a good choice.
>B< Push from Conex Bänninger is a universal fitting that can be used with many different types of tube, thus reducing the inventory costs of professional plumbers. Ideal for retrofit plumbing systems, >B< Push is an excellent choice where space is confined or when heat has to be avoided. Fast and convenient to install, it takes just seconds to create a secure joint. Once connected it remains firm but can be easily turned without becoming misaligned.
Another push-fit option is >B< Sonic, a quick and easy to install flame-free push-fit fitting. Manufactured from high quality copper and brass materials, it is suitable for use with hard, half-hard and soft copper tube and is reusable up to 20 times and recyclable. Suitable for potable water, heating and sanitary applications.
Welding
Welding is perhaps something of a dying ‘art’. It tends to be used on bigger commercial applications with larger sized diameter pipes and involves melting base metals onto the pipes and fusing them together to form a permanent joint. Such joints offer excellent integrity and are ideally suited to demanding environments and critical systems. This technique requires specialised training and equipment and preparation of the joints is vital.
Soldering
Utilising a filler metal with a lower melting point than welding, soldering is most commonly used in residential plumbing applications. It provides good sealing properties in low-pressure applications.
Each jointing solution has its own benefits/advantages and which solution an installer chooses depends on their skill level, competency and comfortability as well as legislation. Therefore, there really isn’t a ‘one-size’ fits all option.