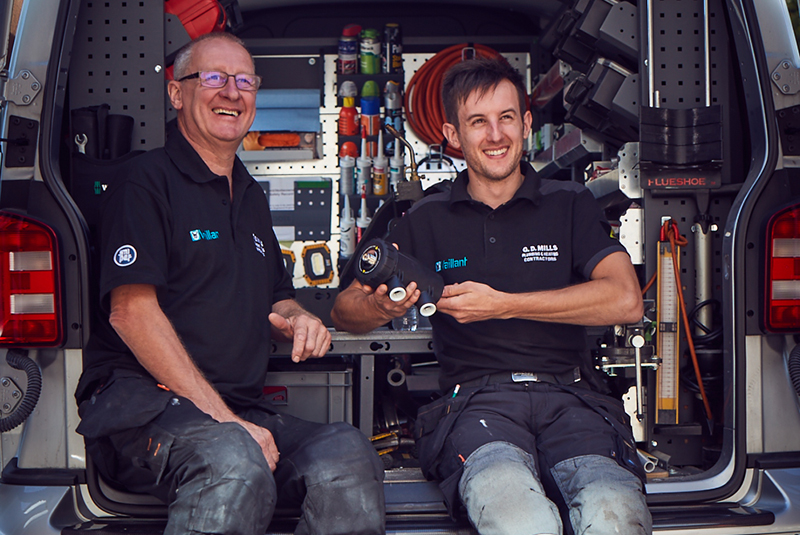
Although poor system water quality is shown to be the single biggest cause of boiler failures (according to Delta EE Independent Research), encouraging customers to stretch their budgets to include water treatment and magnetic filters can sometimes be a difficult sell. Colin Yearp from ADEY caught up with engineer Ryan Mills of GD Mills Plumbing and Heating Ltd, to find out how he approaches this conversation with customers.
Do you see many issues arising from debris in the system?
One of the most common things we see is pressure sensor failures caused by debris in the system. The sensor gets clogged up which tricks it into thinking that there’s no water, so it shuts the boiler down as a safety mechanism.
As boilers are getting more advanced, water quality is becoming even more important. Older systems seemed to cope better with sludge and debris – you might have had the odd few cold spots in radiators – but you didn’t get the same amount of issues. This is because there’s a lot more going on inside boilers digitally nowadays, like the sensors, that can easily get damaged. The ports in heat exchangers are a lot smaller now too, and radiators are generally thinner, so they’re more likely to get choked up. I think customers are also more interested in being efficient nowadays and they want their monthly bills to be as low as possible.
I work for the family business and when my dad was just starting out back in the 70s, power flushing wasn’t a thing, filters didn’t exist, inhibitors were used but you didn’t test for them – there was no such thing as taking water samples back then. My dad remembers when Adey brought out first Magnaclean. He reckons that he was the first person to fit one in Scotland and is convinced that it came directly from Chris Adey! He saw it in a magazine and thought it was a good idea, and has been using them ever since.
What are your top tips to help installers to persuade their customers to invest in preventative maintenance measures e.g. water treatment (flush and chemicals) and a filter?
We always build in the cost of having a filter installed into the quote. We explain how it stops sludge from getting into the boiler and that it’s usually a condition of the manufacturer’s warranty. Most people are happy to be led by us if we take the time to explain it.
It’s the same with flushing the system. We explain that it’s part of the Benchmark system and without it, their warranty could be invalidated. If they decide against it, we just write a note on the Benchmark saying that it hasn’t been flushed, which covers us if they try to question it at a later date.
One method we use to convince the customer is to check the radiators for cold spots with a thermal imaging camera. When they can see it in front of them, it’s visual confirmation that what you’re saying is true and you’re not having them on. It’s a useful tool to show how effective a flush is too, as they can see the cold spots disappearing and the radiator temperature increasing before their eyes.
Do you use water testing systems to ‘diagnose’ problems before recommending a course of action?
We use the ADEY testing kits quite often, especially if we’re quite confident that the customer is going to give us the job, but they just need some visual proof that what you’re saying is true. This is especially useful if a customer has an older system that you know needs flushing, but they say it’s not within their budget. We take a sample, get it tested and say “look – here’s how bad it is”. That usually sways them.
I live in a new build home, so the pipes are made of plastic, and I’ve had a lot of issues with air ingress causing the water to blacken. I’ve treated it with inhibitor and a biocide to stop bacteria growth but the problem keeps returning, so I want to get it tested and find out the root cause. I’ll be trying out the ADEY laboratory testing service and sharing my thoughts on Instagram.
What do you think about changes to Benchmark to include annual water quality checks and top-ups of inhibitors?
I think it’s a good thing but as with any legislation it needs to be enforced, and that’s difficult to do when you’re dealing with private domestic properties.
Some engineers don’t want the hassle so they just write on the Benchmark that the water quality’s fine, even if they haven’t tested it. It’s easy for them to deny responsibility if the boiler breaks down six months later – they’ll just say that it was OK when they last visited. This isn’t great for the homeowner as it can end up invalidating their warranties if they don’t get the system properly cleaned, treated with inhibitor and fitted with a magnetic filter.
What do you usually do during an annual service and how do you quote for it? Do you charge extra for servicing the filter?
We charge a fixed rate for an annual service, which always includes cleaning out the filter and using test strips to check the level of inhibitor. Some people do charge extra for it but we don’t bother, as it’s a fairly simple job, you just need to take it off and wipe it down with a cloth or some Big Wipes. My top tip would be to wipe it down outside and put it into a bin, don’t use a sink or basin or you might find yourself having to scrub it down with bleach to get rid of the stain!