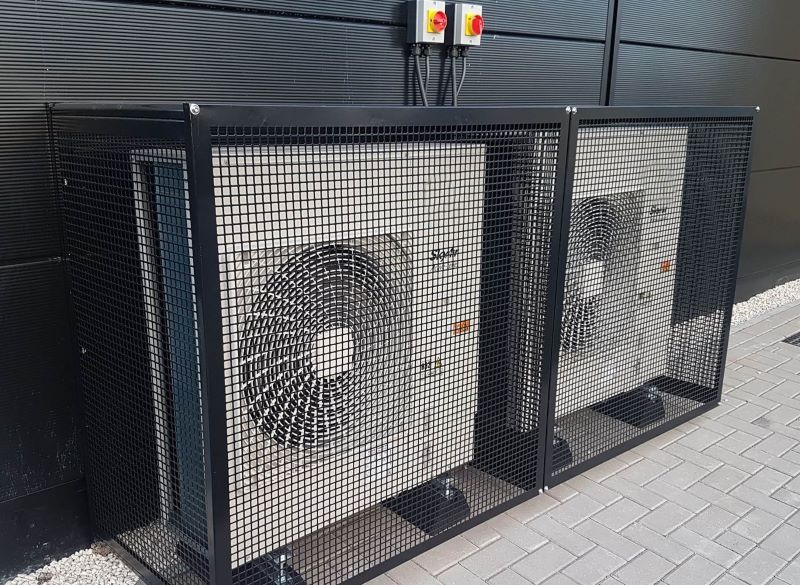
To help installers looking at Air Source Heat Pump installation, Paul Greengrass, Product Development Director from DiversiTech, provides some further tips on installation.
DiversiTech International (formally known as Pump House) has been working in the UK heat pump sector for over 15 years – working with OEM’s, wholesalers, and training organisations to help provide the best installation solutions to deliver heat from the heat pump into the home.
We are a design and manufacturing business which has created a range of installation accessories to assist installers to fit heat pumps in a cost-effective and efficient way.
Efficient heating systems
Air source heat pumps are extremely efficient electrically driven heating systems, with the main power being consumed by the compressor. The standard refrigeration cycle being applied has been used for many years with two key functions compression to produce heat and expansion and evaporation to provide cold.
Through the processes mentioned above, heating of the water within the system can be achieved in an economical manner to provide water to radiators, underfloor heating and for domestic hot water.
Basis of a heat pump
In its basic form, the heat pump acts in a similar way to a boiler – energy in and heating out. However, the key difference (besides that of operation) is that most boilers are typically fitted inside a home while the heat pump sits outside the home (either partly or as a whole).
The heat pump heating cycle provides a coefficient of performance between 3:1 and 4:1, so for every 1kw of electrical energy consumed by the unit the home receives 3 to 4Kw of useable heat (or 300-400% efficiency), as opposed to a gas boiler only achieving around about 92% efficiency.
Are you insulating?
In our previous article we discussed the key factors in ensuring optimum performance air flow and insulating the external pipework.
One way of protecting the external pipework, and more importantly, maintaining the integrity of the insulation around the pipe work is by using external grade trunking. This not only provides important protection to the insulation, but it also improves the aesthetics of the install.
The problem of condensate
Volumes of condensate are being produced by units during the day-to-day operation and defrost cycle. Units can produce up to 50 litres of condensate per day, which equates to approximately 18,000 litres per year.
These volumes are almost double that of a condensing boiler, and taking into account that the unit is installed outside – exposure to cold and freezing temperatures is even more prevalent.
Although not acidic like the condensate from a boiler, this condensate still needs to be routed into a drain or soak away to avoid the risk of ice forming on paths around the unit.
A soak away can be installed under the unit to provide quick draining from the heat pump. The soak away should be installed away from the building to avoid damp ingressing into the footings.
The capacity of the soak away should be similar to that of the boiler soak away as descibed in BS 6798 standards. BS 6798 calls for a 400mm deep hole, 300mm in diameter with a preformed plastic drain tube. If correctly installed the soak away should include around 25kg of chippings to provide adequate drainage. A Geotextile membrane is also recommended to prevent soil and root ingress into the soak away.
Further protection for your install …
If installing air source heat pumps in exposed areas, there is a risk that the outdoor unit can be damaged. In circumstances like these, the installation of protective cages or guards is an option. These protective cages are designed to provide adequate air flow around the unit resulting in the correct manufacturers rear air space.