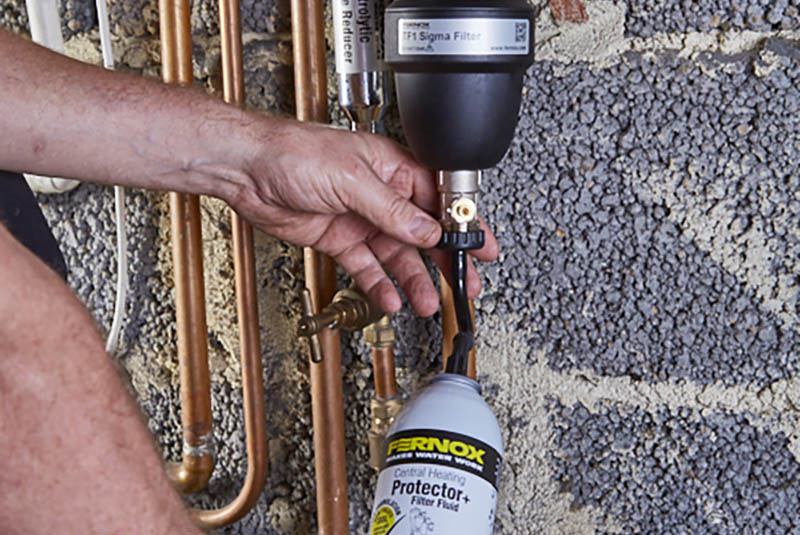
Richard Crisp, Head of Chemistry at Fernox, explains why laboratory testing plays such an important role in central heating system maintenance, and highlights the common issues with problem systems and how to remedy them.
Regular testing of system water should be standard practice for professional installers. The revisions made to BS 7593:2019 place greater emphasis on the importance of system testing and the standard now recommends either re-dosing with inhibitor or conducting a full laboratory analysis of the system water (and re-dosing with inhibitor if required) every five years. However, it has historically been difficult to keep track of samples, especially when working across multiple projects at any given time.
To make the laboratory testing process simple, leading manufacturers offer handy kits that can be used to collect a system water sample and send it to a laboratory for testing. With Fernox, for example, installers can receive a pass or fail result to their mobile (usually within 24 hours of receipt of the sample) via a dedicated, easy-to-use app, as well as a full diagnostic report online or via email, outlining any issues identified and recommendations for how to remedy them quickly.
If a sample does flag a specific issue it is important to get to work quickly to fix it and ensure that no further damage ensues.
Dissolved iron
When steel (which is often used to manufacture system components such as radiators) within the central heating system corrodes, it can lead to the water becoming contaminated with dissolved iron. When this happens, the dissolved particles can oxidise, forming iron oxides which can contribute to debris and sludge. This can cause the system to become sluggish due to blockages in the pipework – and in a worst-case scenario result in component and system failure.
If dissolved iron is present, the system should be cleaned and flushed with a system cleaner like Fernox Cleaner F3 that works to lift and remove contaminants. For heavily contaminated systems Fernox Power Cleaner F8, a pH neutral citric acid-based cleaner, suited to tackle the dirtiest systems, should be used. For the best results, both of these cleaners should be left to circulate for up to seven days (or a minimum of one hour) before flushing, until the water runs clear and the cleaner has been removed.
In some cases, chemical analysis of the water will show that the system water contains cleaner residues as well as dissolved iron. In this case, there is already cleaner in the system, and so flushing should be performed with mains water only.
Once complete, re-fill the system and dose with a high-quality inhibitor like Fernox Protector F1 or, if there is an inline system filter installed, with Protector+ Filter Fluid to stop future corrosion and scale formation.
Hardness deposition percentage
To determine how much limescale is present within the system, lab technicians will often look for the percentage of hardness deposition. Limescale results in inefficient heat transfer, blockages and creates increased boiler noise.
When limescale forms in a heat exchanger, it creates an uneven surface with crevices. Due to the high surface tension of water, water cannot enter these crevices and instead, steam and air bubbles form in the gaps. When the bubbles pop or travel throughout the system, they create noise.
If a lab test identifies limescale as an issue, the system should be descaled by dosing with an acidic cleaner like Fernox DS40 Descaler and Cleaner. It is important to neutralise this type of treatment before disposal to a foul drain to comply with waste regulations, so Fernox provides neutraliser with the product.
After cleaning and once the system has been flushed, drained and re-filled an inhibitor should be added for long-term protection against limescale build-up.