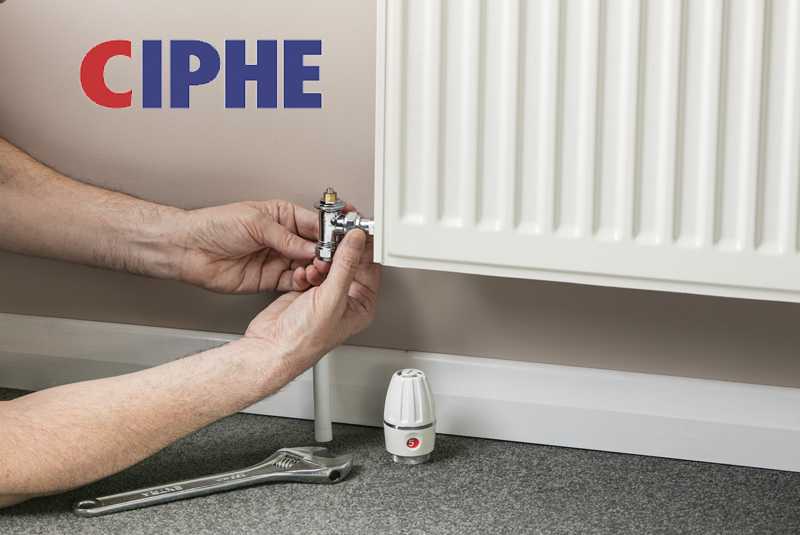
Where energy bills are concerned, TRVs can offer huge savings in comparison to manual valves, but are we achieving the optimum efficiency with every installation? The Chartered Institute of Plumbing and Heating Engineering (CIPHE) talks to Shaun Burrows, a Master Plumber and Senior Technical Support Engineer for Pegler Yorkshire, who discusses how thermostatic radiator valves can make a remarkable difference.
As stated in the CIBSE Domestic Heating Design Guide (2015), the recommended minimum controls that all wet systems must have are;
- Boiler interlock – to prevent the boiler form firing unless a demand for heat or hot water is received
- Thermostatic Radiator Valves (TRVs) – fitted to all radiators except in rooms where a room thermostat is fitted; or solid fuel systems that require a heat leak radiator
- Frost protection – to protect the appliance, system and dwelling
There are also a number of additional requirements for different systems, most of which installers will be familiar with.
It is no secret that TRVs can help to reduce heating costs for the end-user, as was clearly demonstrated by recent research undertaken at the University of Salford in conjunction with BEAMA Heating Controls. By design these valves only allow a radiator to heat to a temperature set by the user, which is monitored and maintained by the expansion and contraction of a thermal element contained inside the head.
The thermal element is most commonly a wax element due to its ability to react quickly to changing conditions. This is the case with Thermostatic Mixing Valves (TMVs), where quick, efficient operation is paramount for safety in order to react accordingly to maintain the users set temperature on the TRV. While the function of TRVs is effectively the same between manufacturers, the manner in which they react varies due to the response time, the differential pressure of the product and hysteresis.
A balancing act
Hysteresis is the value which has been commonly used for many years to measure a valve’s performance. However, it is only when this is coupled with all of the additional product parameters that its true effectiveness and suitability for a system can be determined. To achieve maximum efficiency, it is also important that the system is fully balanced and that the automatic bypass is installed and set correctly.
Essentially, balancing is part of the commissioning process. It is undertaken to ensure that heat from the boiler is being distributed evenly throughout the system and does not offer cold spots or areas where no heat is delivered. The balancing process ensures heat travels evenly through the whole system and does not take the shortest and easiest path. Naturally, heat/hot water will look to travel to the highest point and take the shortest route back to the boiler.
Balancing is a simple process but can be time consuming, meaning many fall back on approximation methods. Such methods include where the lockshield valves (at the highest point of the system) are closed then opened to a quarter of a turn to ensure the system can force heat to other areas of the heating system. This method generally works well for the majority of installations. It does not, however, ensure efficient system operation as there is no consistent differential temperature through the system, which can cause the boiler to cycle more than is required.
Key considerations
To guarantee the differential temperature is maintained throughout the entire system, the differential temperature on the flow and return needs measuring and maintaining at each radiator. This usually means starting with the first radiator on the system and moving on sequentially until the last radiator on the system has been set – with the differential being 10 to 12°C. However, this does not take into account the requirements of a condensing boiler.
For a condensing boiler to operate at its most efficient return, temperatures of 55°C are required – meaning that, in many condensing systems, a differential temperature of up to 20°C can be common to achieve efficient operation.
The requirement of an automatic bypass valve for the system should also be taken into consideration. This is important to ensure system noise is reduced and correct function of all components installed to the system is maintained. It also ensures that excessive strain is not placed on the TRV element when it is attempting to close. While it is correct many combination boiler manufacturers do incorporate these into their boilers, they ask that the installer checks to ensure that it is correctly sized for the system and that an additional, external valve is not required.
It is only when all of the above conditions are correct that the TRV can operate as designed and intended. While many conflicting views exist on the methods, efficient and economic operation cannot be achieved until the system has been commissioned, whichever method is used.
For further information about the CIPHE and work with Pegler Yorkshire, visit www.ciphe.org.uk. For CIPHE membership enquiries, please contact the team via email at [email protected] or call 01708 472791
PHPI’s CIPHE Hub
Stay up to date with the latest news from the CIPHE on the PHPI website at www.phpionline.co.uk/tag/ciphe/… including an archive of articles that have appeared in the magazine, web-exclusive content, and videos from the techtalk live! and smarttalk live! series.