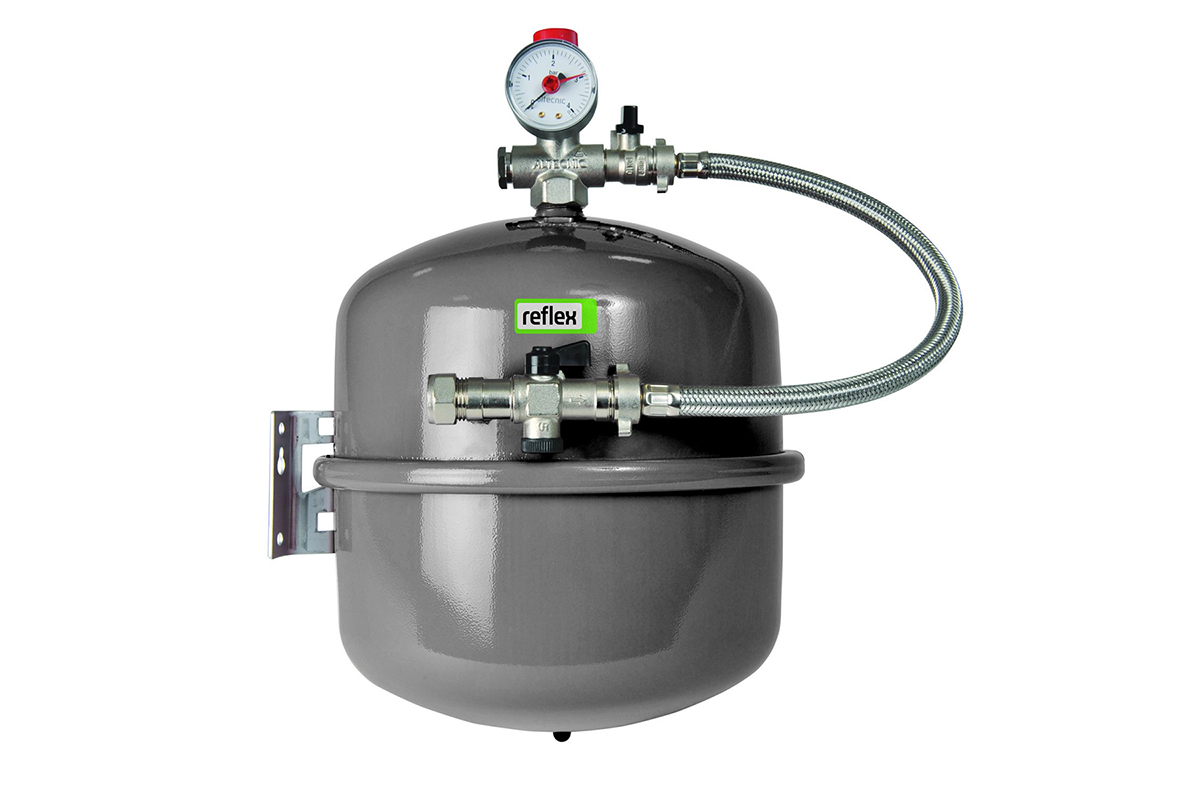
Ed Morris, Technical Manager at Altecnic, explains everything you need to know about sealed systems and their components.
A sealed system is closed to the atmosphere, eliminates the feed and expansion tank as well as associated pipework thus, reducing the risk of contamination, corrosion, and noise in the system.
For a sealed system to operate, it must include all the following:
- An expansion vessel
- A safety relief valve (or pressure relief valve)
- A pressure gauge
- A filing loop
But how does each component work to ensure the system runs efficiently?
Expansion vessels
Lack of expansion leads to unnecessary wear on the pump and other components. Systems may reach critical pressures (usually 3bar) and discharge via the safety valve, not only is this a waste of water but also leads to homeowners calling out engineers or even topping up the system themselves. Constant introduction of fresh water also adds air to the circuit, and this can cause corrosion.
What does an expansion vessel do?
Expansion vessels allow for a higher volume of water to be stored. When water is cold, the pre-charge pressure forces the diaphragm against the tank towards the inlet. As the temperature increases, the expanded water volume pushes against the diaphragm creating additional volume for the water to enter. When the temperature decreases, the pre-charge pressure forces the water from the tank and back into the main heating system. This maintains a constant pressure within the heating system helping to reduce energy consumption.
How do I size an expansion vessel?
It is extremely important for expansion vessels to be sized correctly in order for it to operate correctly and avoid damages. More information on expansion vessel sizing can be found in the CIBSE Domestic Heating Guide.
What maintenance is required for an expansion vessel?
An expansion vessels’ pre-charge gas pressure should be checked regularly as part of a planned maintenance programme. This ensures that the vessel is still operating accurately and is set for the system it is installed on.
Maintenance is made easier when the design and quality of the expansion vessel is prioritised. For example, when a nitrogen-filled vessel is selected for a system rather than a compressed air-filled vessel, the life span of the vessel is significantly increased. This is because oxygen within a vessel can cause the membrane of the vessel to corrode, and any air through the membrane can reduce the pre charge pressure. With a nitrogen-filled vessel (like the Reflex range of expansion vessels), this issue is eliminated.
Filling Loops
Although filling loops are a key element to a sealed system, they are not to be connected permanently to a boiler.
Where is a filling loop installed?
The filling loop is installed between the mains cold water supply inlet and the central heating return pipe in the boiler. After the system has been filled and pressurised, the service valves must be closed, the system isolated and the flexible hose removed and stored until it is used again.
How can a filling loop meet Water Regulations requirements?
To meet Water Regulations requirements, a filling loop should consist of:
- WRAS approved backflow prevention device (a double check valve conforming to BS EN 13959 suitable for protection against a fluid category 3 risk)
- Temporary connecting pipe (a removable flexible hose)
- Service valve (2 isolating ball valves)
- 4 bar pressure gauge (optional)
Safety relief valve
Safety relief valves (or pressure relief valves) are typically used for controlling pressure on boilers in heating systems, on stored hot water cylinders in domestic hot water systems, and in water systems generally.
How does a safety relief valve work?
When the calibrated pressure is reached, the valve opens and, by means of discharge in the atmosphere, prevents the pressure of the system from reaching levels which would be dangerous for the boiler and components in the system itself. By doing this, the safety of a system is maintained, and the system can continue working efficiently.
How is a safety relief valve installed?
Building Regulations state that, where possible a safety relief valve should be installed close to the heat source on the flow circuit. It should be installed in the cold water supply before the water heater ensuring that there are no other fittings or narrowing of pipework between the water heater and the valve.
To comply with Water Regulations, valves should not be connected directly to a drain – the discharge should pass through a visible tundish with an AUK3 air gap and be located adjacent to the safety relief valve, to allow vented water to escape.
Furthermore, the discharge pipe must be the same size as the valve discharge outlet and must not be longer than two metres and have no more than two elbows.
The safety relief valve should be located at a maximum distance of one metre from the boiler.
How can I ensure the safety relief valve remains operational?
To ensure that the safety relief valve remains fully operational and performing to its highest standard, it is important for the valve to be serviced annually. Without this, impurities may collect under the seat of the valve.
A complete solution
Altecnic makes converting from an open vented to a sealed system of any size easy by packaging all the key components an installer needs into a handy ‘Robokit Extra’ available from 8 to 80 litres capacity.
By providing the most high-quality products in a single kit, Altecnic aims to make converting open vent systems to a sealed system easy, especially as we move into the busiest season of the year for plumbing and heating engineers.