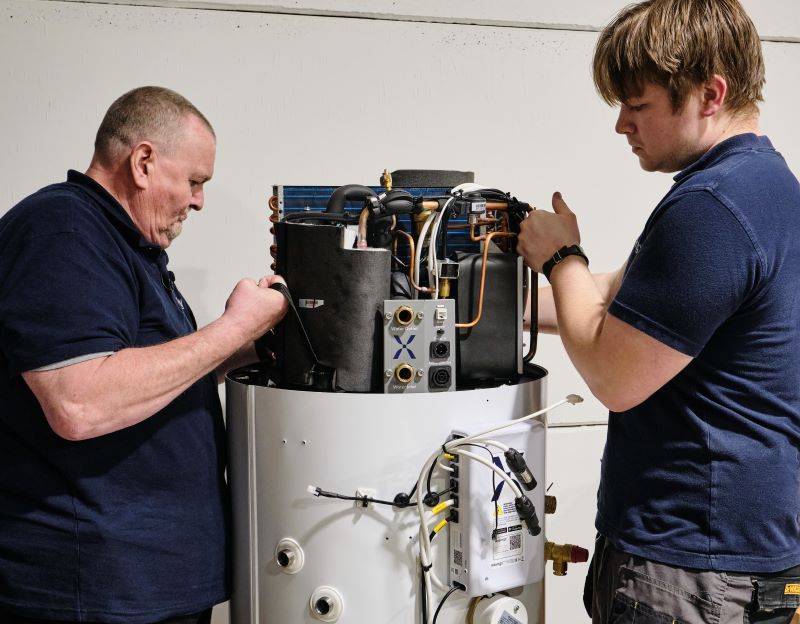
Mixergy Training Officer, Roy Fugler, has been a heating and hot water engineer since he did his apprenticeship with British Gas in 1978 and a trainer for the last 20 years. Recently, he took a moment to describe what installers can expect when they attend Mixergy training with him.
What I love about my job is that every day is different. I meet, either in person or online, heating engineers from all over the UK – and sometimes beyond – each with their own training requirements, so I tailor the days to suit them.
Since joining Mixergy, I have been working with the technical and product team to create some quick guides, videos and e-learning. I’ve also developed some new training presentations and content for face-to-face training which I can deliver either at the Mixergy training centre, partners’ training facilities or onsite.
I have been attending British Gas engineers’ team meetings all over the country, using easy-to-transport demonstration boards to train them on wiring, controls etc for the smart Mixergy cylinders they are installing. They are ‘live’ and working, so the engineers can actually get hands-on, which is a much better way for them to learn, rather than me just talking about it.
Sometimes, a contractor may have engineers working on a new housing development, installing a particular product, or an installer may be fitting one of our products for the first time. In this case I could carry out the training alongside them onsite, sharing installation hints and tips, explaining all the wiring and controls, showing how to connect the cylinder and set up the app, and going through the commissioning process. Then they can carry out the processes on their own, safe in the knowledge I am there to help if they need it.
A brew and a chat
There’s not really such a thing as a ‘typical’ day, but if we have engineers booked into a training course at Mixergy HQ, I tailor the day to suit their needs. They may just install products, or they could be service and maintenance engineers, or they may do both – and there could be a mix of all three, so it’s important I ensure everyone leaves with the information and skills they require for their work.
We start off the day in the only way – with a brew and a chat. If they’ve been signed up for training by one of our area sales managers, I will have had a heads-up of what is required. Sometimes, the engineers have already done a webinar with me but want a bit more in-depth knowledge.
Tea break’s over and we get down to the training. I start off by telling them a bit of background about the company. I explain how, when they were at Oxford University, Pete Armstrong and Ren Kang conceived the vision of a network of smart hot water cylinders which would provide flexibility to the grid. This would enable more renewable energy to come online and support the clean energy transition.
Hands-on
I explain how a Mixergy X smart cylinder works and the differences between it and an ordinary ‘dumb’ cylinder. I talk about how it heats from the top down and uses stratification to only heat the water the household needs.
I cover how to install the cylinders and give an overview of fault-finding and servicing. The delegates can get hands-on with a live cylinder that is connected to a heat pump so I can show them how it works, explain about the gauge and they can get hands on with it.
I show them how to set up the controller – and prove it’s not at all scary – demonstrate how to connect the cylinder to the internet, and also how to set up schedules and temperatures on the Mixergy app.
I also talk about the solar diverter and it monitors the household’s solar PV, automatically diverting excess energy into the cylinder to produce free hot water. I will also show them a Mixergy iHP X integrated heat pump cylinder working and explain how easy it is to install and set up and all the benefits it offers to their customers.
Legislation
During the day, I will cover any relevant legislation and regulations, for example G3 regs, and answer any general questions about heating and plumbing, such as how much hot water is required per person per day.
At the end of the day, I want delegates to leave us knowing that they can install and commission a Mixergy cylinder correctly and having the confidence to talk knowledgeably to their customers about smart cylinders, how they can prepare for the heating systems of the future and the cost and energy savings they can make.
Developing talent
One of my favourites parts of the job has always been working with students. I am passionate about training the next generation of heating engineers. We have a partnership with Newham College in London and I’ve been down there a few times. The College is in quite a deprived area, but the staff are so passionate about getting the students through their courses and exams, and supporting them to enter the thriving renewable heating job market. The staff are really engaging with them and truly helping to make a difference to their lives.
As an industry, we need to encourage more young people to join, particularly with the push for heat pumps, to address the skills gap, add to the number of heating engineers who are moving over to low carbon technologies, ensuring we have plenty of young people entering the industry as more engineers retire.